A supply chain is a collection of steps a company takes to transform raw components into finished products and deliver them to customers. Supply chain management (SCM) is a process that a company uses to ensure the efficiency and profitability of its supply chain and the operations of the firm as a whole.
Stages
One common and highly effective model is the supply chain management (SCOR) model, designed to enable leaders to effectively improve supply chain management practices. The SCOR model has five stages: planning, development, manufacturing, delivery, return. The initial stage of the supply chain process is the planning stage. A plan or strategy needs to be developed to decide which products and services will meet the requirements and satisfy the customers' needs. At this stage, planning should mainly focus on developing a strategy that will maximize profit. After planning, the next step is development. At this stage, the main focus is on establishing strong relationships with suppliers of raw materials required for production. This involves not only identifying reliable suppliers, but also identifying various methods for scheduling delivery, shipping and payment for a product. Thus, at this stage, supply chain managers need to develop a set of processes for pricing, delivery and payment with suppliers, as well as create conditions for monitoring and establishing links. Finally, supply chain managers can combine all of these processes to handle their goods and services. This processing includes accepting and inspecting shipments, transferring them to production facilities, and authorizing vendor payments.
The third step in the supply chain management process is the production or fabrication of products that need to be delivered to customers. At this stage, products are tested, packaged and synchronized for delivery. Here, the supply chain manager's job is to plan all the activities required for production, testing, packaging and preparation for delivery.
This stage is seen as the most metrically intensive block of the supply chain, where firms can assess quality levels, production productivity, and labor productivity. The fourth stage is the delivery stage. Here, the products are delivered to the customer at the designated location by the supplier. This stage is basically the logistic stage, when customer orders are accepted and the delivery of goods is planned. The delivery phase is often referred to as logistics, where firms collaborate to receive orders from customers, set up a network of warehouses, select carriers to deliver products to customers, and set up a billing system to receive payments. The last and final step in supply chain management is called takeback. At the stage, defective or damaged goods are returned to the supplier by the customer. This is where companies have to deal with customer requests and respond to their complaints, etc. This stage is often a problematic section of the supply chain for many companies. Supply chain planners need to find a flexible and flexible network to accept damaged, defective and complementary products back from their customers and to facilitate the return process for customers who have problems with the delivered item.
Functions
Office of quality customer service. This is the first function of supply chain management. It refers to the procurement of raw materials and other resources required for the production of goods. This requires coordination with suppliers to deliver materials without any delays and alignment of all processes in the chain for successful operation.
Operations
The operations team is responsible for planning and forecasting demand. Before placing an order for the supply of raw materials, the organization must anticipate the possible market demand and the number of units that need to be produced. Accordingly, it also sets up ball movement for inventory management, production and delivery. If demand is expected, this could lead to excess inventory cost. If demand is expected, the organization will not be able to meet the demand of the customers, resulting in a loss of revenue. Thus, the operational function plays a critical role in supply chain management.
Logistics
This supply chain management function requires tremendous coordination. Food production started. It needs storage space until it is sent for delivery. This requires the creation of local warehouse agreements. Let's say groceries must be delivered outside of a city, state, or country. This results in being carried in a loop. There will also be a need for storage on the terminal. Logistics ensures that the products are reached of courseth delivery without any interruptions.
Resource Management
Any production consumes raw materials, technologies, time and labor. However, all processes must be efficient and effective. This phase is taken over by the resource management team. He decides to allocate resources to the right activity at the right time to optimize production at reduced prices.
Information Flow Management
Information exchange and dissemination is what actually supports all other supply chain management functions. If the information workflow and communication is poor, it can break the entire chain and lead to mismanagement.
Logistics and an Integrated Supply Chain
This is a process in which each phase from the procurement of raw materials to production, quality control to packaging, distribution or delivery for final delivery is monolithic and inseparable. This is a holistic list of various processes that may be under the full control of one company or several partners who have united to collectively control an integrated process. Supply chain integration has several benefits, which is why most companies have switched to integrated supply chain management.
Supply Chain Management in Organizations
Supply chain management in an organization is essential to the overall success of a company and customer satisfaction. It includes all activities that lead to success from the beginning of planning, management of all activities and sourcing operations to procurement and logistics (transport, warehouse management, inventory management, etc.), marketing operations, as well as coordination and cooperation. between all parties involved in the supply chain of suppliers (outsourcing) and service providers and customers.
Vertical Integration
This is the process of extending your control to different levels of production. You can use reverse integration, forward integration, or both, depending on your resources and target achievements.
Horizontal Integration
This is the expansion of a business at the same point in the supply chain, either in the same industry or in a bordering one. The company can achieve growth through internal expansion. This can happen when a retailer increases the variety of products they sell in a particular category. For example, a barbershop that sells a limited number of shampoo brands might add other brands to their shampoo offerings to appeal to a wider and diversified customer base.
Merger
The company can also provide horizontal integration through external expansion. This is achieved by merging with another company at the same stage of production. This could allow the company to achieve diversification into additional but diverse product markets. However, if the products that the companies sell are similar, the merger is considered a merger of competitors. A merger is called a monopoly when all manufacturers of a particular product or service are merged and an oligopoly when most of the manufacturers are united in several large alliances.
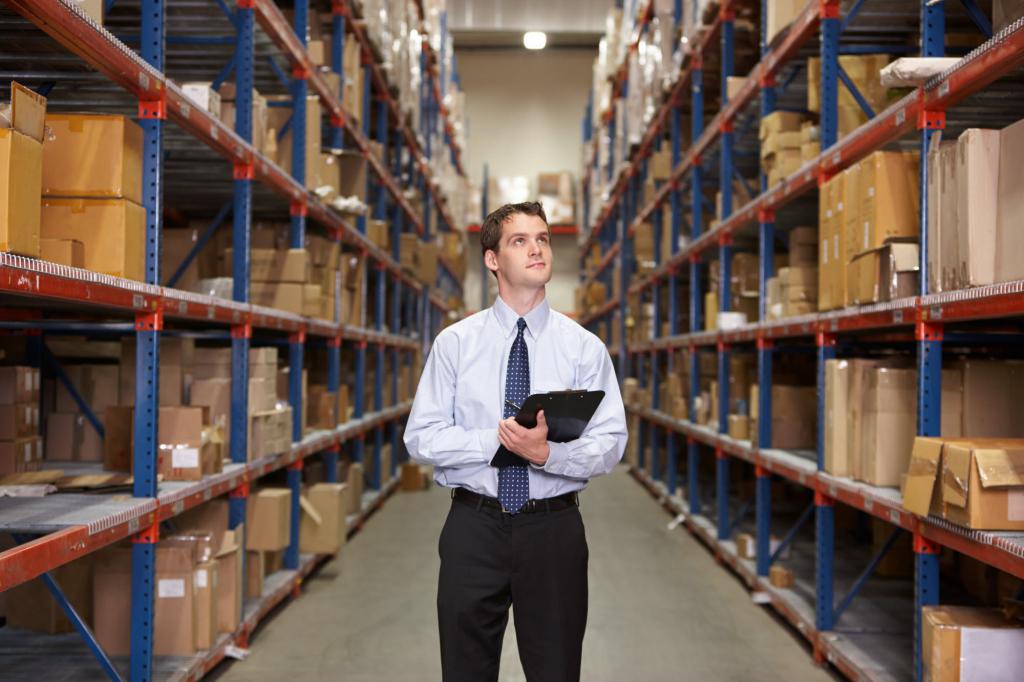